
- #MESHLAB FIX NON MANIFOLD MANUAL#
- #MESHLAB FIX NON MANIFOLD SOFTWARE#
- #MESHLAB FIX NON MANIFOLD PROFESSIONAL#
Optimization: This step isn’t always necessary and may vary depending on the type of 3D printer you’re using.Re-modeling : If both of the above steps don’t work, you’ll probably need to re-edit the 3D model using CAD or other 3D modeling software.If problems persist, you can try re-meshing the entire model or use options such a “make solid” or “shrink wrap” (depending on the tool). Then, choose options to fix other geometry issues. Start with repairing holes or gaps in a way that preserves your 3D model.
#MESHLAB FIX NON MANIFOLD MANUAL#
#MESHLAB FIX NON MANIFOLD SOFTWARE#
This may be good enough in some cases, but certain images will need more in-depth improvements, and professionals may opt for very advanced editing software to get the quality they want (short of re-shooting).

Repairing STL files can be very similar to repairing photos. Photo editing tools often have an automatic option that fixes an image with a single click. Related to this, an STL may describe enclosed volumes that are too thin to be printed practically.įixing these types of issues is better described as an optimization step rather than repair, although both are often be handled by the same software. For example, attempting to represent hair or fur might result in an enormous STL (because of the many triangles required to represent such a “surface”), which is hard to process due to details smaller than a printer’s resolution.

There’s a thin line between an STL that has actual errors in its mesh and one that has a correct mesh but describes something that’s still hard or impossible to print. Triangles may also overlap or intersect in a way that is hard or impossible to interpret. Some STLs can contain floating triangles that shouldn’t be present. Unless these two shapes are eventually interpreted as one object, your printer will have difficulty printing them together. This can be a mind-bending concept, but consider how a modeling program might represent two intersecting cubes. A related problem occurs when an edge or vertex is shared by one or more shape. The way these shapes (or the “shells” of these shapes) are joined is important and, if done incorrectly, can hinder slicing. In this article, we’ll quickly cover the most common types of issues you might encounter, explain how they can be repaired, and then compare several of the best tools to make even the most wayward of STLs printable.Ī printable design must contain closed, non-overlapping volumes (Source: Sculpteo)ģD models usually consist of combinations of different shapes.
#MESHLAB FIX NON MANIFOLD PROFESSIONAL#
They range from free, hobbyist-friendly tools through to complex, commercial tools designed for professional use. That’s where STL repair tools come in, helping you to identify and fix these issues, resulting in a model that is manifold.
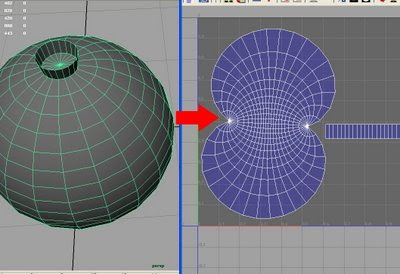
For example, a wall with 0-mm thickness can exist in software but not on your build plate. In an abstract, CAD environment, where models are created, almost anything is possible, but the same can’t be said in the real world, where models are printed. Whatever the exact reasons, the root of these issues often lies within the mesh of connected triangular faces and vertices that STLs use to represent 3D models. If you’re 3D printing, you’ve probably encountered the dreaded “unprintable STL” problem: Your STL file looks fantastic, but it causes your slicer problems or results in strange misprints or just complete failures.
